How to Evaluate Logistics Properties: How Companies Can Focus on What Matters in Site Selection in Infill Areas
Key Concepts
In determining how such companies can best evaluate and select sites, I propose four key concepts:
Focus on what characteristics of a property will support the company’s mission and objectives. The property amenities and features that matter vary significantly from company to company. Developing the company’s specific requirements is critical for choosing a property that will support its goals.
Qualitative assessments matter. Quantitative assessments are those you can measure and therefore are often given priority. However, don’t dismiss the importance of qualitative assessments. Important metrics such as employee satisfaction and productivity are strongly influenced by qualitative aspects of a property.
Keep off-site characteristics in mind. Freeway access, incentives, labor, utility rates, retail amenities, traffic patterns, railroad crossings, road quality, proximity to residential areas, and construction projects can greatly impact a company’s operation. Yet none directly describes a potential site.
Evaluate a site on its positive and negative characteristics. Many site selection projects focus on positive attributes of properties without considering the potential risks the company might encounter during occupancy. Creating awareness around property characteristics that may negatively impact an operation is required for a wholistic approach to site selection.
Current Environment
The incredible growth in ecommerce in the last several years has fueled an unprecedented amount of demand for logistics real estate in the United States. Now, more than ever, a company’s success or failure depends on finding and securing real estate that will support their supply chain and, ultimately, their company mission.
However, it is increasingly difficult for companies to find logistics real estate that will help them achieve their objectives. In the last five years North American Industrial vacancies have been cut in half, from around 10% in 2010 to just under 5% in 2019. Net absorption over the last five years is the strongest five year period in the past twenty years.1
Companies generally add space through two distinct routes. The build-to-suit, where a property is designed and improved to its specifications, requires available developable land. In infill areas, where developable land is scarce, build-to-suits are typically not an available avenue for the logistics firm to add space. Therefore, they must evaluate and choose between a set of improved options.
If we accept that existing logistics real estate is scarce and subject to strong competitive demand, it is in the best interest of any company requiring such space to efficiently evaluate, select, and secure the best available option for their company.
Off-Site Considerations
Off-site considerations refer to qualities that influence the desirability of a site, but are not on the property itself. They are some of the most important factors in site selection because they often cannot be modified or improved.
Companies should define and weigh the off-site factors that are most important to the project’s success as part of defining their real estate requirements. While off-site factors will vary, certain factors are usually weighted heavily for certain types of uses.
Common Distribution Off-Site Factors
Distribution uses would include ecommerce, warehousing, crossdocking, and transportation industries. Properties supporting distribution uses should have off-site factors that facilitate the movement, assembly, and storage of inventory such as the following:
Access to Freeways
Access to freeways are usually measured by the drivetime to the nearest on and off ramps, and alternative on and off ramps, for each freeway in reasonably close proximity to the subject site. A freeway is a roadway where all access is controlled via elements such as grade separation and on and off ramps. In tertiary markets, a highway or major road is sometimes substituted since there may not be a freeway in the area.
Proximity to Key Locations
Drivetime or distance to one or more key locations. For example, companies who use a significant amount of parcel delivery may want to locate in close proximity to a parcel carrier hub. Other common examples include being close to a key customer or supplier.
Reasonable Traffic
Traffic is a key factor in drivetimes. While ESRI and other GIS mapping software can estimate drivetimes, driving main routes to and from a prospective site at peak traffic is a great way to confirm drivetime estimates.
Road Construction
Identifying current and future road construction projects that may impact drivetimes to and from a location should be part of any site due diligence. While major freeway projects are usually infrequent, they can be significant disruptions to traffic and access to a certain area.
Railroad Crossings at Grade
Rail crossings at grade can cause delivery delays and tardiness by employees. A best practice is identifying any rail crossings that are in proximity to a site that cannot be traversed above or below grade on an alternative route.
Cost of Doing Business
Taxes, utility rates, prevailing wages for employees, and license fees are some examples of a cost of doing business in a certain area. Certain cities can be more or less friendly to distribution uses. In infill areas it is not uncommon to encounter warehouse taxes, moratoriums on distribution uses, and conditional use permits which add to the cost of doing business.
Common Manufacturing Off-Site Factors
Manufacturing uses would include any use involved in the transformation of less-finished to more-finished goods. We can also include non-manufacturing uses that employ large amounts of people in this category since those uses will often share important off-site factors. Properties supporting manufacturing uses should have off-site features that attract and retain employees, meet power and infrastructure requirements, and offer a competitive advantage in lower operating costs such as the following:
Labor Costs and Availability
The available labor pool and prevailing wage to staff and employ an operation is a key factor in any employee intensive operation. Turnover is also another important metric that may lead some operations to locate in areas with higher unemployment levels or labor competition.
Incentives
Prospective operations with large numbers of anticipated employees and significant capital expenditures typically receive the greatest amount of incentives from public agencies. Manufacturing uses typically include incentives as an important off-site factor to consider in their site selection process.
Proximity to Retail Amenities
Proximity to restaurants and other retail locations can be helpful in recruiting and retaining employees, and a potentially needed alternative to a company lunchroom.
Cost of Doing Business
While such costs can often be reduced through incentives, utility connection fees, utility usage rates, employee benefit laws, right to work, business licensing and permitting, and taxes are just some of the costs that are typically important to manufacturing uses.
Access to Public Transportation
Finding a site with a bus or train stop nearby is important for companies with employees who depend on public transportation to get to and from work. Some large manufacturing operations will offer their employees a shuttle service from the nearest public transportation hub or housing area.
Training and Talent
Modern manufacturing often requires skilled labor, sometimes requiring advanced degrees or certifications. Areas that can offer a large pool of qualified professionals or training opportunities are often looked upon favorably.
On-Site Considerations
On-site considerations are amenities or elements contained within a property or in close proximity to its location. Unlike off-site factors, on-site factors can often be improved with money and enough lead time.
Common Distribution On-Site Factors
Properties supporting distribution uses should have on-site factors that facilitate the movement, assembly, and storage of inventory such as the following examples:
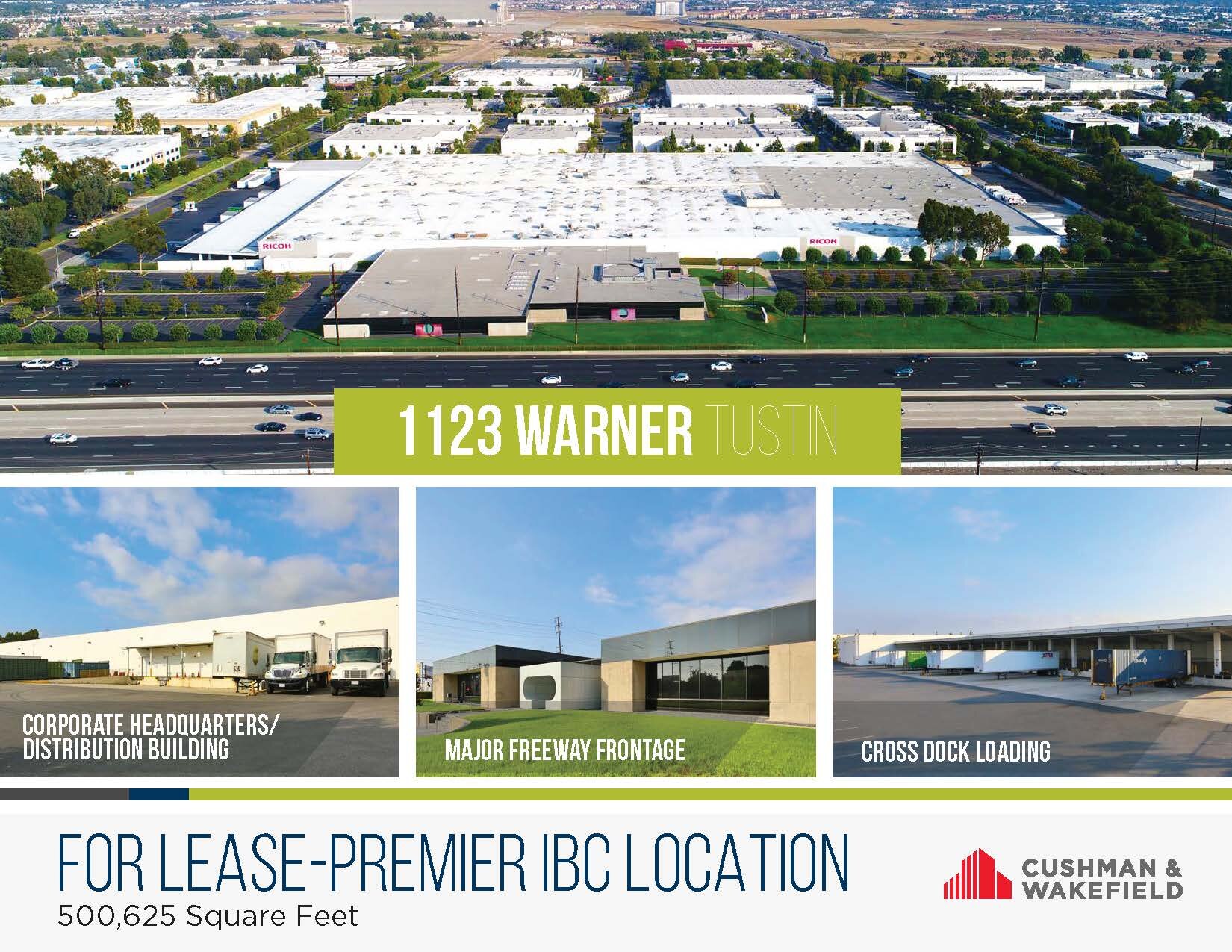
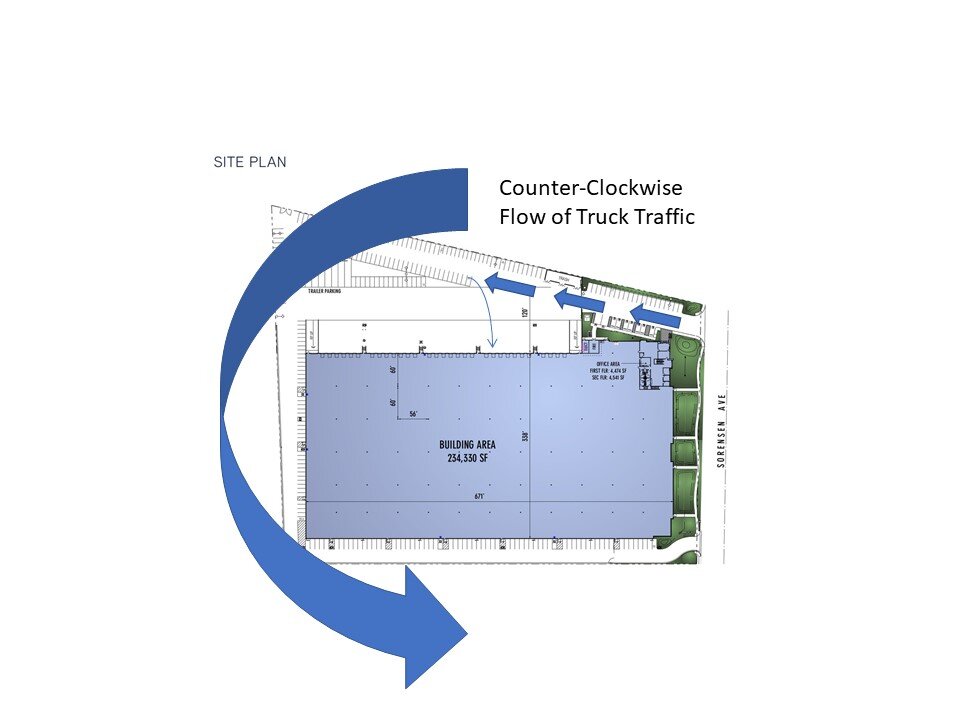
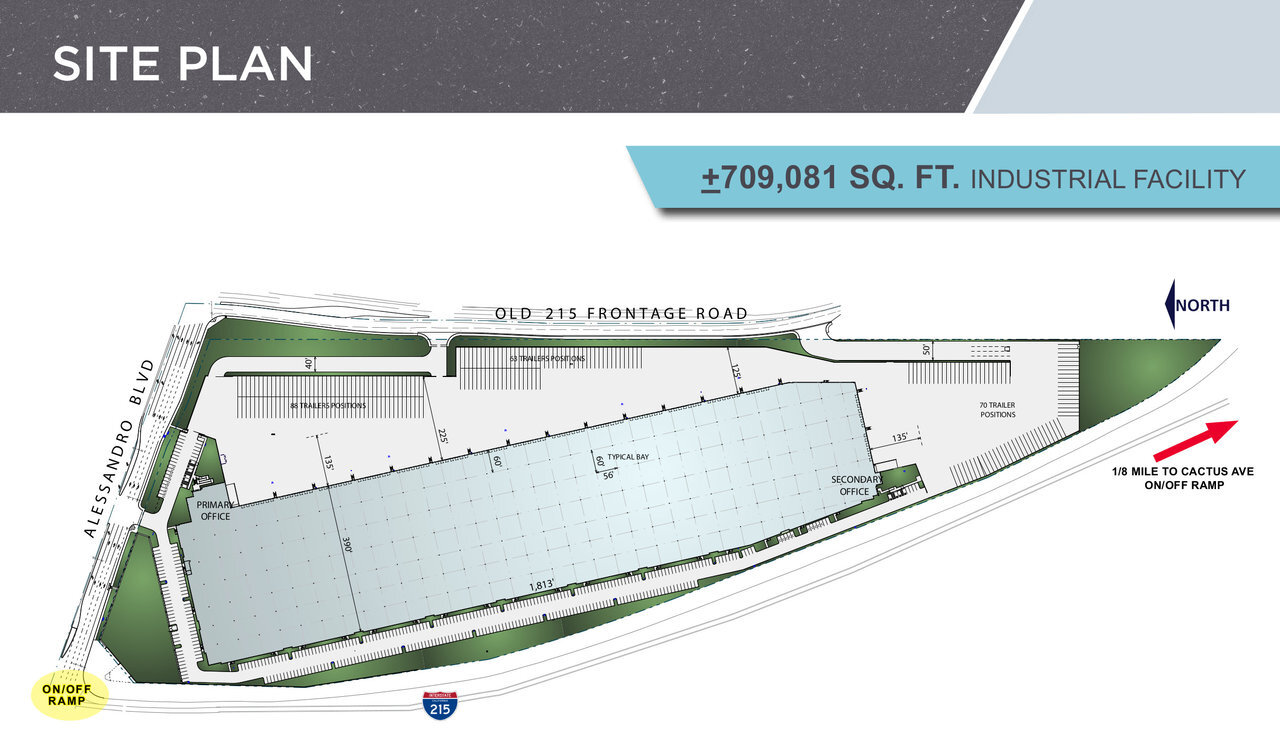
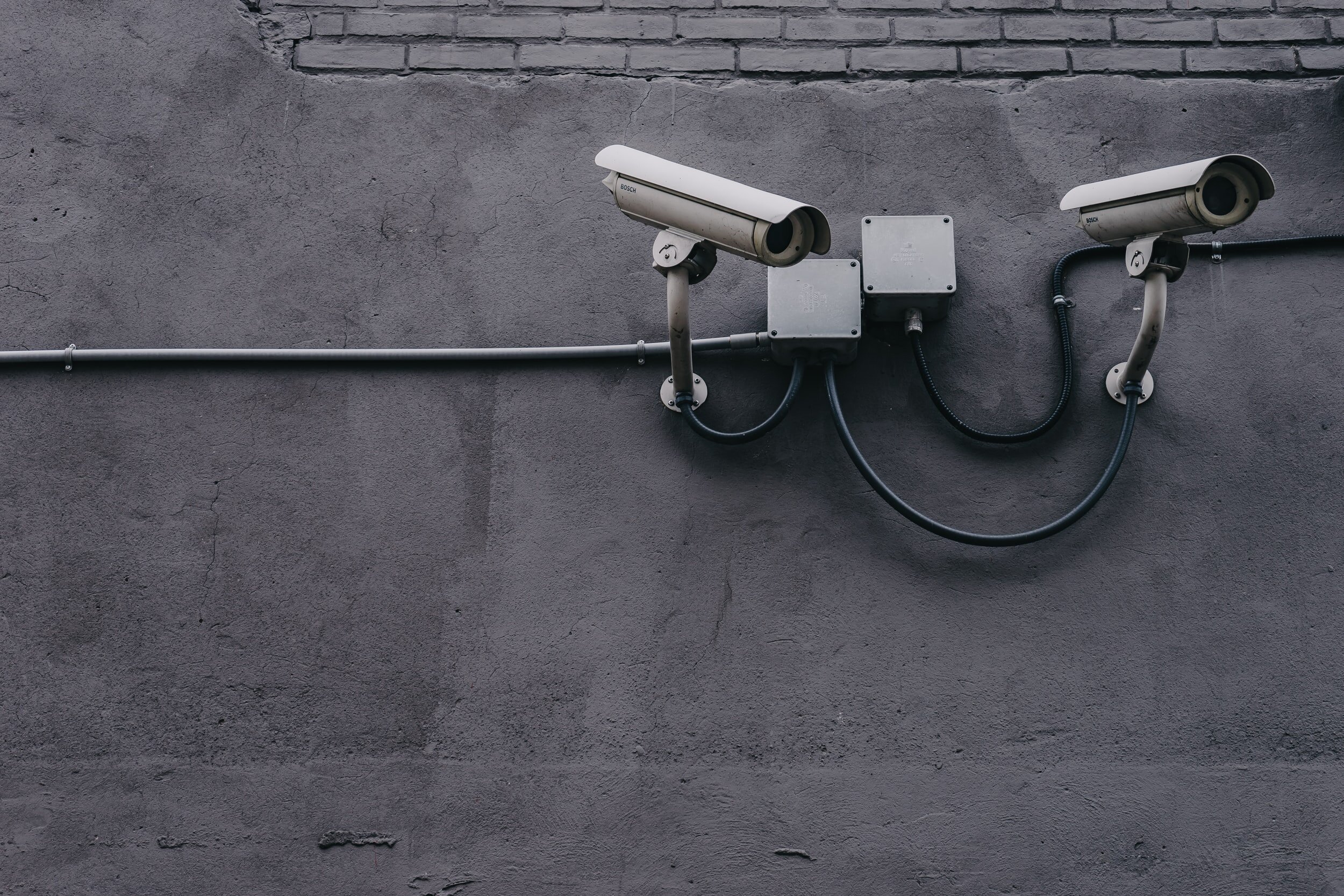
Advertised Amenities
Advertised amenities are the features that are highlighted or presented on property marketing material. These typically include features such as clearance height, sprinkler systems, bay spacing, building dimensions, office square footage, dock positions, and more. It is critical that prospective tenants or buyers independently verify information contained in marketing materials. This is especially true for any building system that is vital to the success of the operation.
Ingress and Egress
Ideally access driveways would have the ability to turn right or left, and enter from the right or left from a low traffic street. Medians without turn lanes can restrict left hand turns on roadways into the property and exiting the property. Trucks and automobiles accessing high traffic streets may have difficulty exiting the property during peak hours.
Wide Driveway Entrances and Throats
Driveway aisles, called throats, should be wide enough for each inbound and outbound lane to contain a 8’ 6” wide Class 8 tractor and trailer with buffer spacing. City building codes will often limit driveway widths to under 40’. The driveway in the slideshow above has likely obtained a variance since its driveway throat is over 45’ at its narrowest point and the City code where it is located limits driveways to 35'. 2
Separate Truck and Automobile Driveways and Parking Areas
At least one separate drive aisles and parking areas for commercial trucks and automotive vehicles can improve ingress and egress, increase truck yard efficiencies, and lower incidents between employee outside entity vehicles. Drive aisles to other properties should ideally not impede on-site loading activities.
Image
A high image building that appears to be well maintained is a good indication of a quality landlord and occupant. The opposite is of course true.
Circulation of Trucks
To increase visibility for a truck driver to back a trailer into a dock high position, truck traffic should ideally flow counter-clockwise into the loading areas.3 When the driver is on the left side of a cab, reversing and turning using the left mirror or over the left shoulder is easier for a truck driver than a “blind” reverse and turn using the right mirror.
Truck Yard Depth and Trailer Parking Areas
Commercial tractors and 53’ trailers require a minimum of 131’ to back into a dock with trailers on either side of it, assuming the dock door is 13’ on center.4 Any trailer parking areas should have a concrete landing strip approximately 20’ wide, starting 40’ from the end of the stall to 60’ from the end of the stall.5
Condition of Parking and Yard Surfaces
The condition of the parking and truck yard areas is important for any occupier to evaluate because of the significant cost of repairing and replacing asphalt or concrete. A best practice is to ask the owner for written evidence of the most recent repair work and most recent replacement or installation of any asphalt or concrete areas. Even if the landlord is responsible for the cost of maintaining the parking and truck yard areas, repairing or replacing large areas can disrupt operations.
Significant cracking in asphalt or concrete is a potential warning sign that similar damage could appear elsewhere even if the above area is repaired. Ultimately, when acquiring a property, occupiers should use their best efforts to avoid taking responsibility for pre-existing issues.
Loading Areas
In addition to the typical information found in marketing materials, such as the number of dock positions and ground level doors or ramps, occupiers should also visually inspect the loading areas for the following:
Size and condition of the loading apron, the surface area where trailers will be backed into the dock high positions. Ideally loading aprons will be a concrete surface stretching a minimum of 60’ from the dock in order to support trailer legs and the rear wheels of a tractor when parked.6
Condition of the loading doors and dock equipment. I like to look for any gaps at the bottom of the doors when they are closed because it is an indication the door has damage, even if it is not visible from the exterior. In addition, dock equipment, such as dock bumpers, edge of dock levelers, and pit levelers, should appear to be in good condition.
The dock height, especially for older buildings. In new construction, the standard dock height is 48” from the ground to the floor. However, dock heights vary from building to building.
Security
Existing security features are often important on-site factors to occupiers. Site control, fencing, gates, guard houses, and security systems can be important requirements for certain operations. Site control, where the occupant does not share any contiguous area or access with another company, and fencing can often be disqualifying or expensive if they do not already exist. In addition to on-site security features, locating near residential areas can also be considered a security risk.
Warehouse Floor Damage
As with surface condition in parking and yard areas, the condition of the surface of the warehouse floor is also an important on-site consideration for distribution uses. Prior to occupancy, any damage to warehouse floors should be fully repaired because the damage will likely only get worse with use.
Common Manufacturing On-Site Factors
Properties supporting manufacturing uses should have on-site factors that attract and retain employees, meet power and infrastructure requirements, and offer a competitive advantage in lower operating costs such as the following examples:
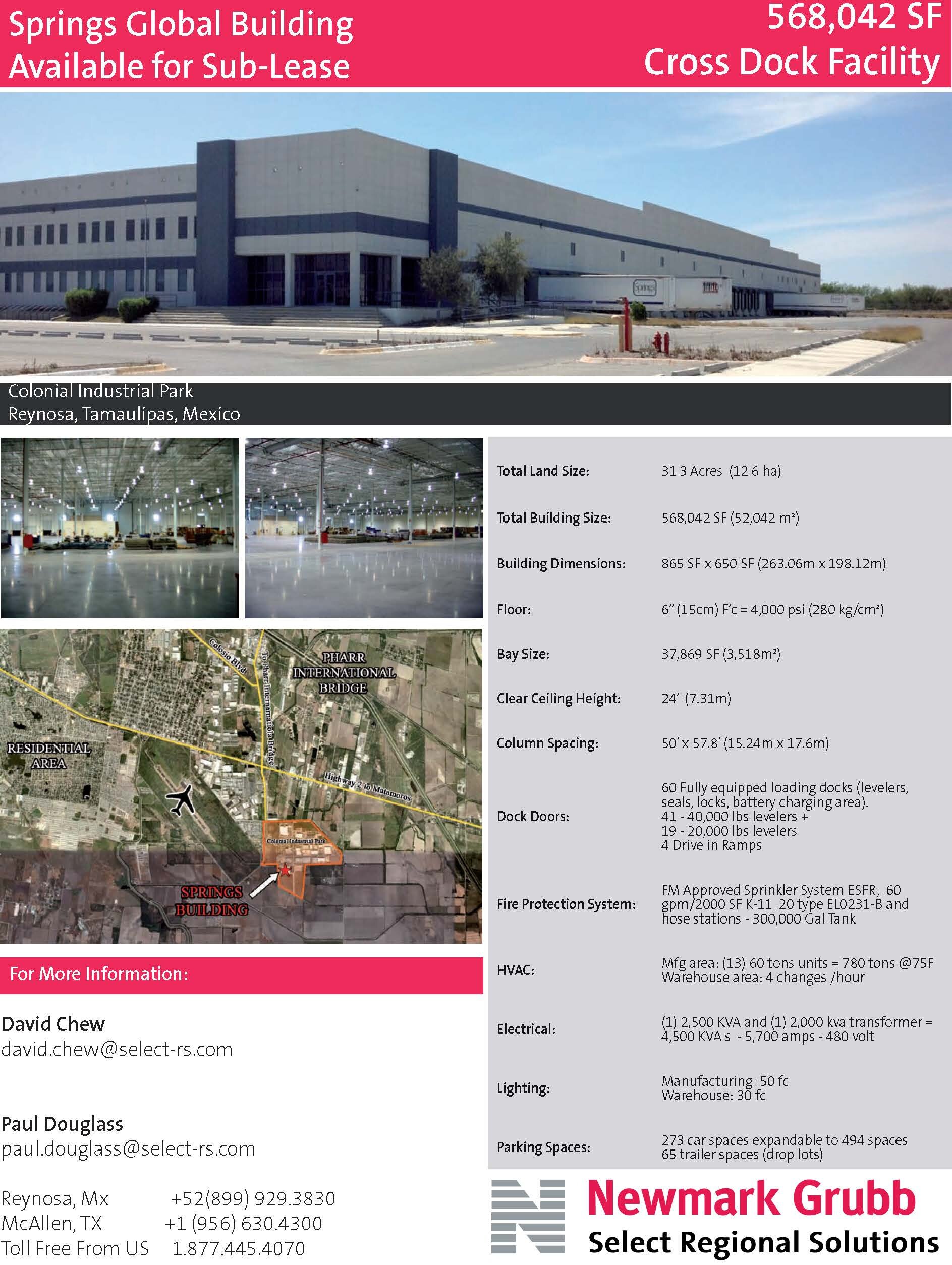
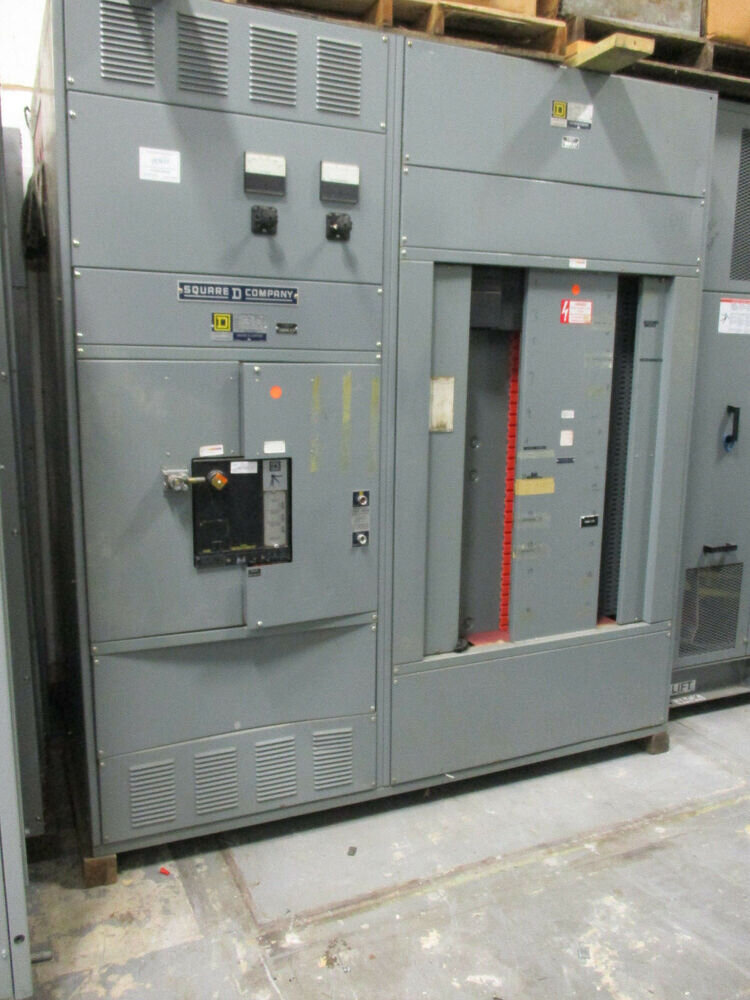
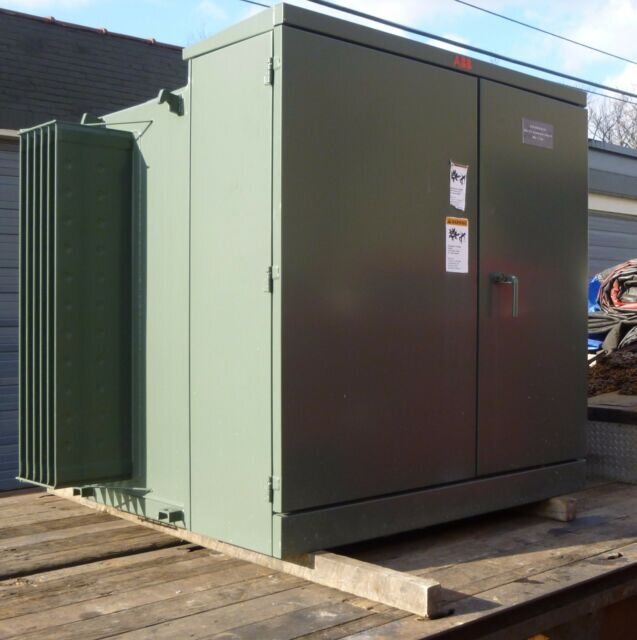
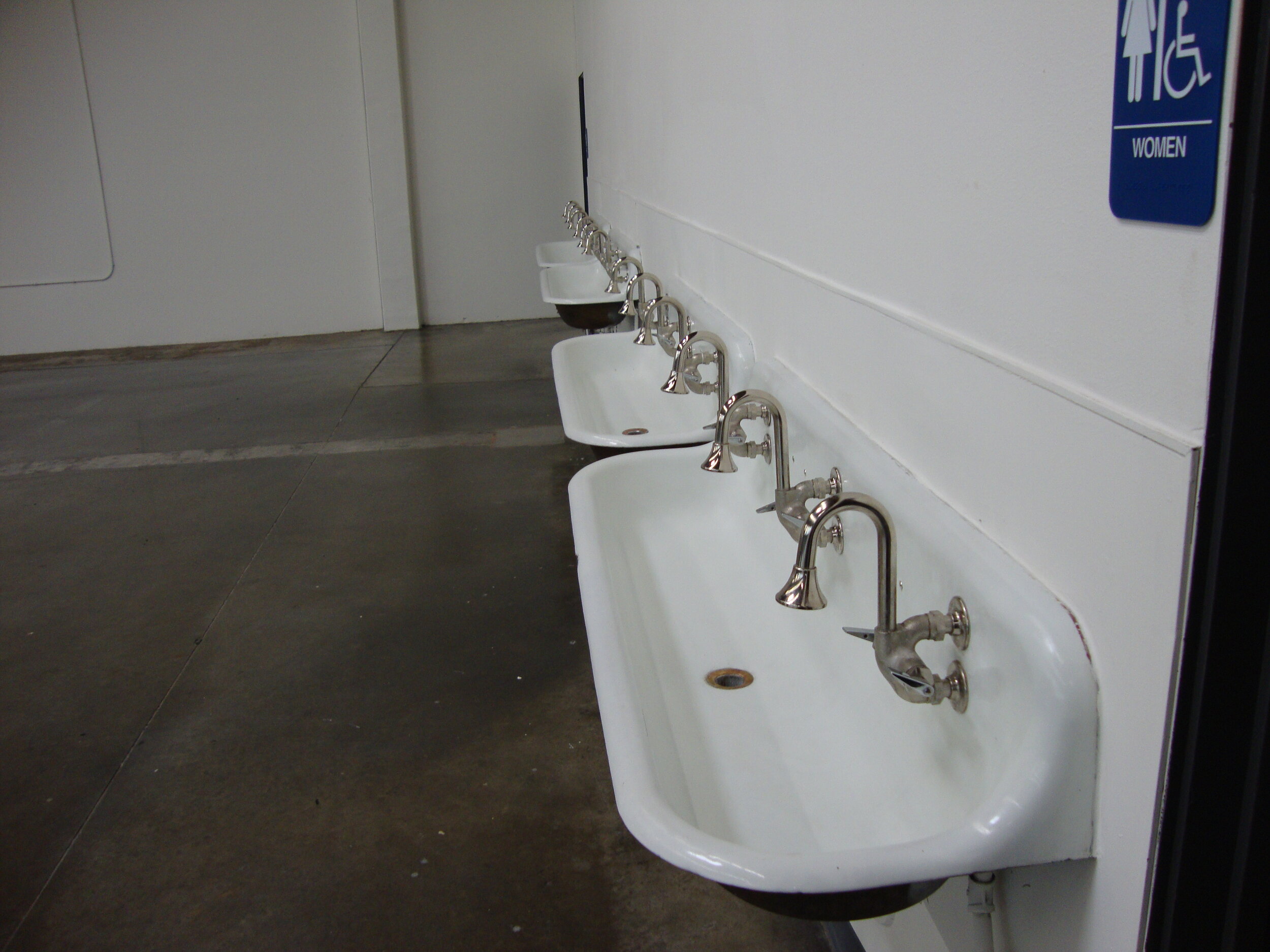
Advertised Amenities
Manufacturing requirements often have more variance from project to project than distribution requirements, but there are several on-site factors that are common. The number of parking spaces, foot candle of lighting, electrical supply, HVAC in manufacturing and warehouse areas, bay size, floor loading capacity, and building dimensions are often important on-site factors for manufacturers.
Cafeteria, Lunch and Break Rooms
Projects with large employee counts typically require cafeterias, lunch rooms, and/or break room facilities.
Power
Electrical power is often at the top of the list of important on-site factors for manufacturing operations. Power is commonly marketed by the capacity of the switchgear panels. Modern panels are typically 480 volt 3 phase 4 wire and are rated by the maximum amperage that can be supplied to them. As I have mentioned, marketing information should be verified and power is absolutely no exception to this rule. Companies should have a qualified electrician confirm all aspects of power in a building prior to an acquisition. In addition to the capacity, occupiers should confirm the supply to the switchgear panels. They can do this typically by having their electrician contact the power company to confirm the transformer size and conduit size leading into the switchgear panels.
Safety Law Compliant
Safety is an important objective in any industrial operation but especially so in manufacturing operations. Companies should confirm on-site factors are fully compliant with any required codes and regulations.
Restrooms and Locker Rooms
Restroom capacity is another important on-site amenity for manufacturing uses. In many municipalities there are a certain amount of restrooms required for each male, female, and gender-neutral employee. Insufficient restrooms not only may be a code issue, but can lead to employee turnover and dissatisfaction. For companies that require uniforms, protective clothing, or no personal property on a shop floor, locker rooms are often required to allow employees to change and keep their personal possessions secure.
Just Hit Go! today to discuss this post or any other commercial real estate matter I can assist you with!
Endnotes
1 Cushman & Wakefield
2 City of Buena Park
3 HPA and NAIOP
4 HPA and NAIOP
5 HPA and NAIOP
6 HPA and NAIOP